Constructing a new building or renovating an existing building can be an exciting process, particularly watching your goals take shape throughout the course of the project. The excitement builds as it nears completion, and your goals are no longer just plans on paper but a tangible reality. One of the final steps in any construction project that involves a new HVAC system is commissioning the system and running testing, adjusting, and balancing or TAB. As we are finishing up construction of a new Law Enforcement Training Center (LETC) in North Little Rock, Arkansas, let’s follow along and peek in at the commissioning and TAB process.

1.     Initial Planning and Design
The LETC is a 23,500 sq. ft. facility with classrooms, administrative offices, secure storage rooms, and IT/communication spaces. During the design phase of this project, the project team assessed the building’s heating and cooling load based on factors such as the size, orientation, insulation, and occupancy. With this information, they selected the appropriate type and size of HVAC equipment, mapped out the most efficient duct layout for even air distribution, and ensured the design adheres to building codes and energy efficiency.
The HVAC system selected for the LETC is functional, durable, and energy efficient, enhancing occupant comfort while making maintenance easy to perform. The heating system includes two high-efficiency natural gas hot water boilers. Heated water is piped throughout the building to provide preheat at the air handlers and reheat at the variable air terminal boxes.
For air conditioning and ventilation, a variable air volume (VAV) air handler with chilled water cooling supplies conditioned and ventilation air to VAV terminal boxes throughout the building. These provide zone level control via air volume dampers and hot water reheat coils, allowing adequate airflow to the space for ventilation without overcooling.
The system also includes enough mechanical redundancy to ensure backup support and capacity.
2.     Installation of Equipment
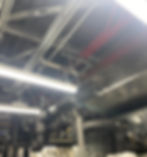
The construction phase included the actual installation of the HVAC system including equipment, ductwork, piping, and wiring. Thermostats and building automation systems (BAS) to manage temperature and humidity were also placed. At LETC, each zone has its own thermostat / humidistat for local control. In addition, high occupancy spaces such as classrooms and conference areas are equipped with carbon dioxide (CO2) monitoring to reduce ventilation requirements for the space when the room is at less than full occupancy. The main air handling unit also has a UV disinfecting light at the main cooling coil to prevent microbial growth.
3.      Commissioning and TAB the System
The next step for LETC’s HVAC system is completing commissioning and TAB, meaning the system is started up, checked for functionality and optimized for performance. Commissioning is performed by third-party commissioning agents who:
Inspect all components for leaks, proper connections, and correct electrical loads.
Power on the system to verify that it heats, cools, and ventilates as designed.
Test safety systems to ensure the equipment shuts down correctly in case of malfunction.

Commissioning begins with equipment start-up and pre-functional checks (PFCs). Once PFCs are completed, performance verification tests begin, and, at the same time, the critical phase of TAB. TAB ensures the HVAC system operates efficiently, meets design specifications, and delivers comfortable indoor conditions throughout the building. Like commissioning, TAB is performed by a third-party firm.
Testing
In the testing phase, technicians measure the performance of the system’s components, including:
Airflow testing: Technicians measure air velocity and volume at various supply and return registers to confirm the correct amount of air is being delivered to each room.
Temperature and humidity testing: Temperature readings ensure that the system maintains setpoints throughout the building, while humidity levels are verified for comfort and compliance.
Static pressure testing: Static pressure readings in ducts help identify obstructions or leaks that could reduce system efficiency.
Adjusting
Once initial tests are completed, adjustments are made to the system to optimize performance:
Damper adjustments: Dampers within the ductwork are adjusted to balance airflow between different zones.
Fan speed calibration: Fans may need to be adjusted to ensure proper air circulation throughout the building.
Control adjustments: Thermostat settings or BAS controls are fine-tuned to ensure accurate temperature regulation.
Balancing
The final step in TAB is balancing, which ensures that air is distributed evenly and in the correct amounts to each space:
Airflow balancing: The air delivery to each space is fine-tuned to meet the design specifications. This ensures that no rooms are under- or over-conditioned.
Zone balancing: For buildings with multiple zones, balancing ensures that each area receives the right amount of heating or cooling according to its unique needs.

Once all these steps are complete, a Certificate of Readiness is signed and functional performance tests (FPTs) can be performed. The final step of commissioning includes review and verification of all the test results. Then, a Final Commissioning Report is issued, and the building systems are deemed fully commissioned. Ross Group also provides instructions for routine maintenance, essential for keeping the new HVAC system running efficiently and extending its lifespan.
Commissioning and TAB are essential steps for every facility to ensure HVAC systems are fine-tuned for comfort, energy efficiency, and reliable performance. Whether it’s a training center or an office building, a well-commissioned system will provide years of optimal performance for your facilities.